Cal/OSHA Sonicu White Paper
If you are looking for Sonicu’s heat stress monitoring system to help you become compliant with Cal/OSHA’s heat stress regulations as they expand nationwide and it helps you and your team eliminate manual logging, improve compliance readiness, and protect all your temperature-sensitive assets, you’ve arrived at the right place.
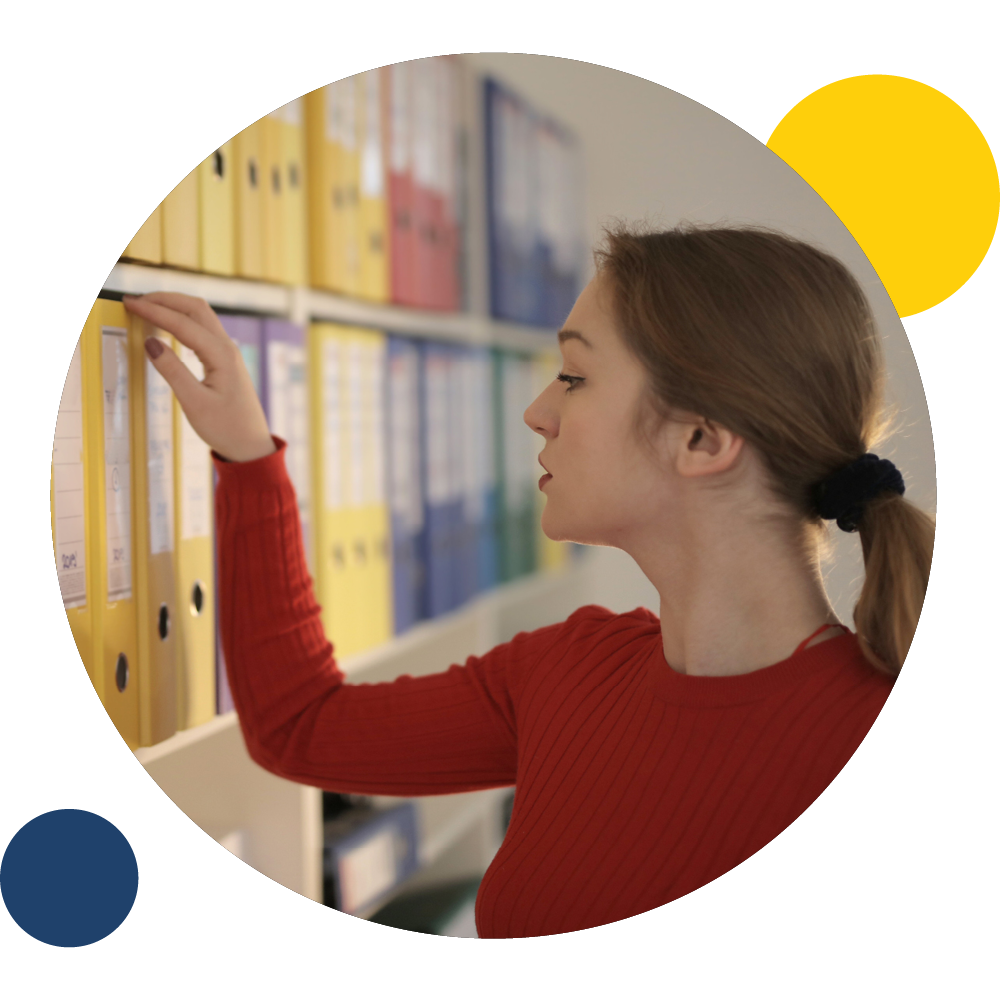
Let us help you evaluate your needs!
- Safety: Alerts to protect assets
- Compliance: Automated reports
- Efficiency: Reduced Manual Logging
And what makes us different?
- Lifetime Warranty: Never buy hardware again!
- Unlimited Users: Scale across your entire org
- Connectivity Flexibility: Wi-Fi, Cellular or Data Hub
- Phone call alarms: Alerts won't get ignored
- Mobile App: 500 Freezers in your pocket
All American made and supported!
See What Customers Say About Sonicu
Asset Protection. Compliance Automation. And Reduced Manual Processes.
Sonicu serves thousands of professionals at hundreds of organizations across North America by improving how they monitor and manage their most sensitive assets and environments.
Professionals from healthcare, life science, laboratory and cold chain facility management turn to Sonicu to help them improve the way they do business.
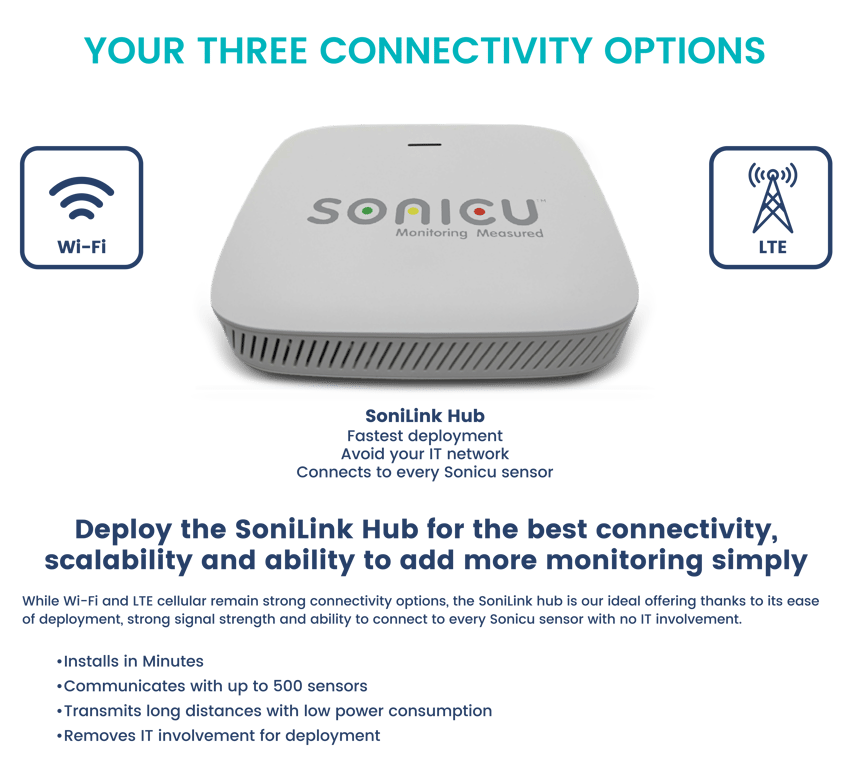
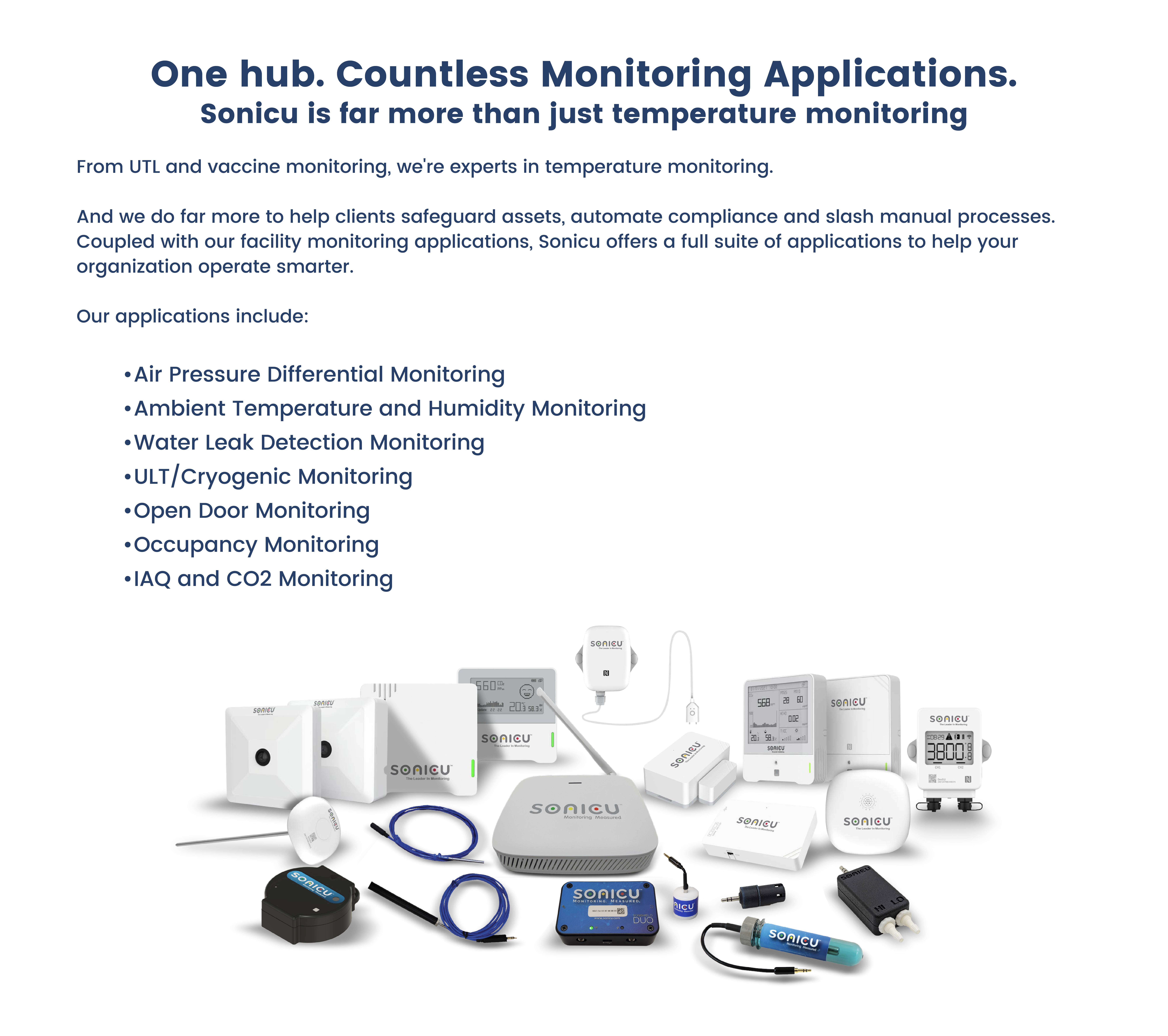
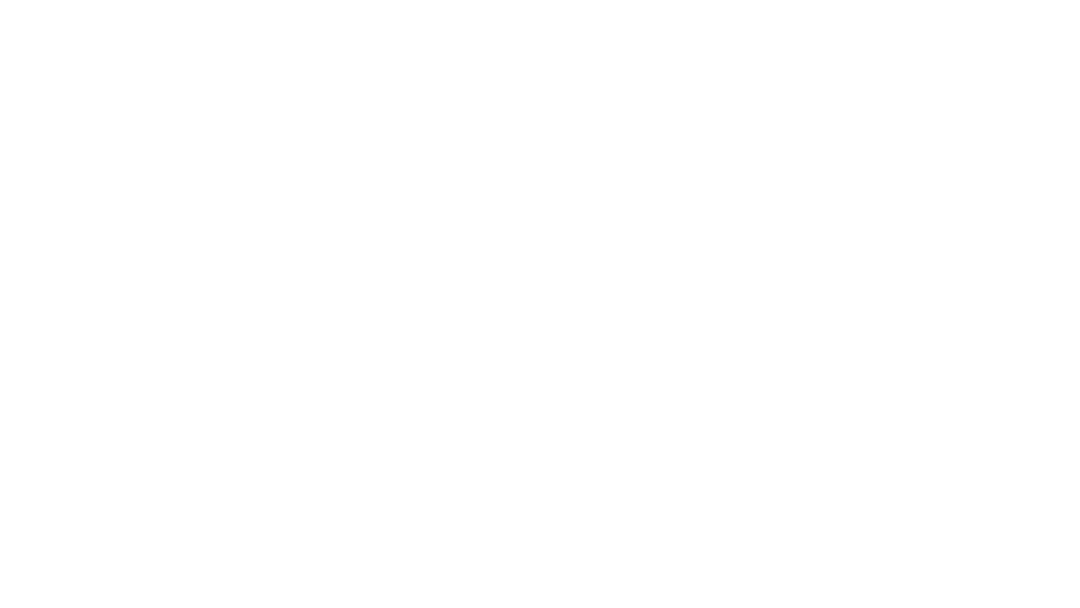
Heat Stress Regulations Expand Nationwide
Some of the finest names in healthcare, including Indiana University Health, University of Michigan Health System, and Stanford University rely on Sonicu to provide a robust and continuous environmental monitoring system, including temperature, humidity, air pressure, and more.
These respected healthcare and research brands turn to Sonicu for four primary reasons:
- Real-Time Monitoring: the sensors collect temperature, humidity, air pressure data, and more, and transmit it wirelessly to SoniCloud - our cloud-based platform.
- Operational Efficiency: Virtually eliminate the need for tedious and costly manual logging
- Compliance Automation: Respond to any regulatory audit or inspection in a few clicks with our reports section
- Asset Protection: Detect and respond to any threshold that can threaten anything perishable: food, drugs, vaccines, research, etc.
Our customers stay with us thanks to our American-based customer support, which is never more than a phone call away. While our technology is intuitive and powerful, we know it’s only as strong as the people who stand behind it.
How California is setting the pace for a new wave of OSHA regulations designed to protect workers from increasing heat challenges
A new raft of federal OSHA regulations focused on protecting workers from indoor heat stress is prompting health and safety professionals to quickly adopt new processes and technologies to stay compliant.
These indoor heat stress regulations are being deployed nationwide with uneven rigor.
Even in states where high temperatures are the norm, regulations may be inconsistent – for example, Nevada is ramping up worker heat stress protections, while Florida is actively blocking their implementation.
This lack of uniformity may be remedied by federal OSHA policy, yet it remains unclear how enforcement and corrective action will be executed to help national organizations adhere across sites in states with potentially vastly different regulations.
Nevertheless, one state is marching ahead with rigorous compliance requirements that have prompted action from health and safety leaders.
California, where the state’s occupational health and safety organization has rolled out an aggressive set of heat stress regulations, is setting the standard for heat stress regulations.
In any workplace, employee safety is of paramount importance, and increasing heat can pose a serious threat to workers – amplified in states such as California that are prone to high heat and temperatures for much of the year.
As our world continues to warm, this challenge is expected to increase and present new compliance requirements for employers of all sizes and shapes.
While the Occupational Safety and Health Administration (OSHA) is in the process of developing new sets of regulations and guidelines at the federal level, the state of California has moved ahead and laid out its own rules aimed at keeping workers safe in the face of increasing frequent high temperatures and real risks posed by heat.
While both OSHA and California strive to mitigate the risks associated with indoor heat stress, the immediate risks posed by California’s climate have prompted the state to enact regulations intended to curb heat injuries (and potentially even deaths) experienced by workers in environments such as:
- Construction job sites
- Warehouses
- Commercial kitchens
- Manufacturing areas
- Agricultural & other outdoor settings
- Logistics and repair shops
- Confined spaces
Importantly, California’s regulations are aimed at workplaces that experience temperatures in excess of 82ºF. In unconditioned facilities located inland from the cooler coastline, many businesses are having to adjust to the reality of better tracking and responding to increased indoor temperatures.
Sonicu has quickly transitioned from supporting from a handful of heat stress customers with our simple and affordable heat index monitoring solution to dozens as organizations look for a trusted monitoring application that can help them comply with the the Golden State’s rigorous new standards.
Tyner Pond has entrusted Sonicu and received these top features:
- American-based Customer Service and Tech Support
- Redundancy of Power/Connectivity to protect data integrity
- SNAP calibration service for NIST compliance
- Hardware assembled in the United States
- Built on AWS Cloud for simplicity, speed, reliability, and scalability
We have the experience and make it easy to deploy our S-Series sensor and communicate with SoniLink hubs to collect data and access the temperature data on SoniCloud via either a desktop web-based interface or on the industry-leading mobile application.
A vast array of factors ranging from harsh sunlight to high humidity to scorching desert heat in varying climates across the state means temperatures can easily soar far above the benchmark of 82ºF in indoor environments.
In light of this, California has deployed stringent mandates and suggestions for employers seeking to bring their facilities and operations into compliance with the new regulations.
Some of these are infrastructure-centric, including:
- Improving ventilation and airflow in warehouses and confined spaces
- Implementing effective cooling systems to regulate environmental conditions
- Providing personal protective equipment (PPE) to employees to aid in cooling
- Using natural and artificial cover to provide shade and relief from hot sun
- Infrastructure to support employee hydration (water stations, etc.)
California’s regulations also call for compliance measures that are less infrastructure-based and more focused on the administrative side, including:
- Recommendations for adjusting schedules and strenuous working hours to avoid dangerous heat at the hottest times of day
- Extensive training to ensure employees and supervisors know the dangers of heat and recognize when an environment is unsafe for employees
- Training personnel to prevent, recognize, and treat heat-related maladies such as heat exhaustion, heat stroke, etc.
- Training personnel in proper and thorough reporting of heat-related incidents
- Mandating employees to take breaks for rest and hydration
Risk assessment and analysis of dangerous conditions are essential, yet they are insufficient independently.
To make this a more useful reference for operators improving their compliance plans, the California report lays out some extra steps to help employers.
Administrative methods include:
- The creation and regular updating of an Indoor Heat Illness Prevention Plan (HIPP)
- Mandating workers take breaks for hydration, rest, and time out of the sun or hot environments
- Continuous monitoring of environmental working conditions
- Sonicu is currently working with scores of California businesses to deploy our simple and affordable indoor heat stress monitoring solution designed to meet this regulation
- Heat stress monitoring need not be expensive or complex with our battle-tested hardware, intuitive software, and U.S.-based customer support
- Implementing both human and technological monitoring methods (i.e. supervisor monitoring, temperature sensors, automated alarming and alerts)
- Scheduling based on weather, sun exposure, and/or other predictable heat trends in a given environment
These regulations and measures are the end product of previous heat-related accidents, tragic missteps, and experiences that have been meticulously reported by a multitude of personnel in various workplaces over the years.
While these tragedies could have been prevented, their importance as lessons for current and future employers is paramount.
In addition to heat stress monitoring, Sonicu plays a vital role for organizations in other industries such as Ohio University and others including:
- Healthcare: Nurses respond to our alerts to keep your medicine safe
- Life Science/Lab: Lab directors rely on our alerts to protect priceless research
- Universities: Research and science department heads rely on our alerts to keep research and classroom labs safe.
- Food Service: Food distributors rely on our tech to protect your dinner
The Importance of Detailed and Reliable Record-Keeping
Both OSHA and California regulations repeatedly stress the importance of detailed, thorough, and replicable record-keeping, especially in the event of a heat-related injury or death.
Meticulous record-keeping can provide numerous benefits, such as:
- Ready access to facts and information for investigators, employees, and other parties involved in any incidents and their aftermath
- Opportunity for a detailed review of events, decisions, and circumstances leading up to a heat-related workplace incident
- Providing ample opportunity to turn yesterday’s mistakes into tomorrow’s lessons
Employees must receive extensive and adequate training when it comes to record-keeping and documenting mishaps in the workplace.
Shortcomings, successes, and decisions – both good and poor – must all be documented so as to properly inform a detailed prevention plan.
For its part, OSHA’s vision of the future indoor workplace closely aligns with the regulations California has set forth.
Some of Washington’s OSHA guidelines aimed at improving worker safety include:
- Implementation of Indoor Heat Illness Prevention Plans (HIPPs)
- Cooling PPE requirements
- Monitoring protocols to ensure safe working environments
Both OSHA and California place emphasis on the idea that employees at all levels of the organization must receive extensive training to recognize, prevent, and manage heat-related dangers and adverse effects.
However, preparedness and compliance efforts are only one aspect of this report, and OSHA also focuses on what some of the financial ramifications of implementing these regulations may be.
OSHA’s analysis includes an evaluation of costs such as:
- Improving existing heat-reduction infrastructure in facilities (shade areas, ventilation, fans, HVAC systems, etc.)
- Implementing new heat reduction infrastructure where none currently exists
- Hefty penalties and fines may be levied against employers who continue to operate out of compliance with new regulations
- Lawsuits, settlements, and other fees that may arise as a result of employee complaints, injuries, or death
OSHA and California both understand that, for smaller employers that operate on a thinner margin than their larger competitors, these compliance costs can be devastating and may lead to significant operational challenges.
In the long term, however, OSHA compliance is designed to deliver:
- Safer working conditions
- Smoother, more efficient production
- A reduction to (ideally) zero employee lost time due to injury and other mishaps
Halting production and/or day-to-day operations due to workplace emergencies results in time wasted, money lost, and potential negative ripple effects throughout supply chains, production lines, and organizational structures.
Of course, employees and personnel required to work in regulated environments will see immense benefits as a result of these mandates, such as:
- More comfortable working conditions
- Likely improved productivity
- Reduced healthcare costs following heat-related injury and trauma
- Fewer breaks in production resulting in docked pay, altered schedules, and forced time off
When it comes to workplace injury, the margin for error is zero, and both reports are essentially seeking to eradicate the preventable suffering of employees working in high-risk zones.
You can learn more about how our software helps compliance professionals in these case studies:
Discount Drug Mart: Power Outage Protection + Compliance Automation
Problem: Transitioning from manual temperature logs and reactive power outage management
Solution: Adopting Sonicu's advanced system for seamless temperature monitoring and real-time power outage alerts across its 77 locations.
Hendricks Health: From Nutrition to the OR
Problem: The need to improve compliance and safety across various departments, starting from nutrition to the operating rooms.
Solution: Upgraded monitoring systems to enhance patient safety and streamline compliance across multiple facilities.
IU Health: Enterprise Monitoring
Problem: Challenges of using a locally based server and multiple monitoring solutions across departments.
Solution: Transitioned to a single, cloud-based solution with Sonicu to enhance monitoring capabilities across more than a dozen locations and the IU School of Medicine.
Employers must be proactive if they are to implement appropriate preventative measures, such as ensuring that the workforce of any given employer has extensive training and a solid grasp of the latest heat-related policies.
This is the reason both California and OSHA are placing such an emphasis on training and prevention.
If operators and employees alike can evaluate and assess a certain environment beforehand, the likelihood decreases that individuals will enter into it and be caught unaware of dangerous heat, humidity, dehydration, and other related dangers.
Hence the importance of employees, administrators, managers, supervisors, and staff at every level receiving training in recognizing, preventing, and treating heat-related injuries. Knowing the signs and symptoms and recognizing them in one person can lead to a rapid reassessment of working conditions and might even save lives.
Additionally, employers and industry professionals must interact regularly to better share methods for controlling heat-related calamities.
This can occur through:
- Engaging with industry groups to discuss emerging compliance measures
- Following industry publications and leaders to stay abreast of emerging trends, best practices, and regulatory news
- Close analysis of any new regulatory documentation and/or legal proceedings
Both California and OSHA’s reports are designed to be detailed and descriptive in their requirements for compliance.
However, owners and senior leaders must engage with regulatory bodies to confront potential confusion.
By doing this, employers may become aware of new and emerging methods for monitoring and compliance that they may otherwise never have known about.
In sum, both sets of regulations emphasize the importance of compliance to enhance worker safety.
Employers are urged to prepare by developing comprehensive prevention plans, investing in workplace controls, and providing comprehensive training for their workforce.
As extreme weather events increase, heat-related death and injury will, unfortunately, rise with the temperatures if compliance measures such as these are not closely adhered to.
Organizations of all shapes and levels of technical sophistication can turn to Sonicu for simple and affordable heat stress monitoring technology that is already trusted across California and many other states.
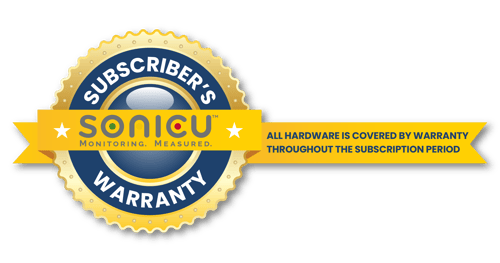
American-based Customer Support: Robust & Reliable High Touch Service
Software and technology is only as good as the people who stand behind it.
At Sonicu, that means our team of American-based customer success managers who are never more than a phone call away to help field and fix any service issues.
Our probes and sensors are placed in demanding frozen environments and our software literally sends billions bits of data monthly, meaning there’s always the potential for a hiccup on either the hardware or software.
We are committed to fielding every customer service request promptly and addressing our customer’s concerns promptly and professionally.
“I like to say that every refrigerator or freezer is like a car in that they all behave a bit differently,
and then every now and then you just get a bad boy who doesn’t want to perform as we need it to,”
Martha Rardin, Director, Nutrition and Dietetics, Hendricks Regional Hospital.
“Sonicu has been a powerful tool to identify which units are behaving out of spec and get our team
to fix them before we have a serious issue.”
Tim Livesay, Director, Hancock Regional Hospital Pharmacy Director
How IU Health
consolidated all of its pharmacy monitoring needs
into one cloud-based platform serving dozen of locations.