Cleanroom Environmental Monitoring
If you’re looking for a cloud-based air pressure monitoring sensor solution that eliminates manual logging, improves compliance readiness, and protects all your clean rooms and compounding rooms, you’ve arrived at the right place.
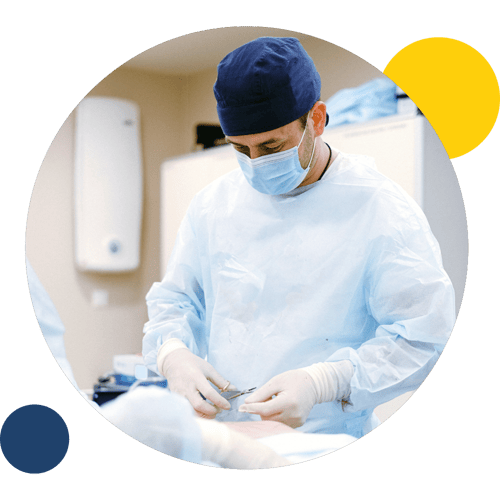
Let us help you evaluate your needs!
- Safety: Alerts via text, email, push notifications and phone calls to protect your precious assets
- Compliance: Automated compliance reports
- Efficiency: Reduced Manual Logging and time spent on reports
And what makes us different?
- Lifetime Warranty: Never buy hardware again!
- Unlimited Users: Scale across your entire organization
- Connectivity Flexibility: Wi-Fi, Cellular or Data Hub
- Phone call alarms: Alerts won't get ignored
- Mobile App: 500 Freezers in your pocket
- Facility monitoring: Simple to add water leak, door open, occupancy, and even IAQ monitoring
Engineered in Indiana with U.S.-based support.
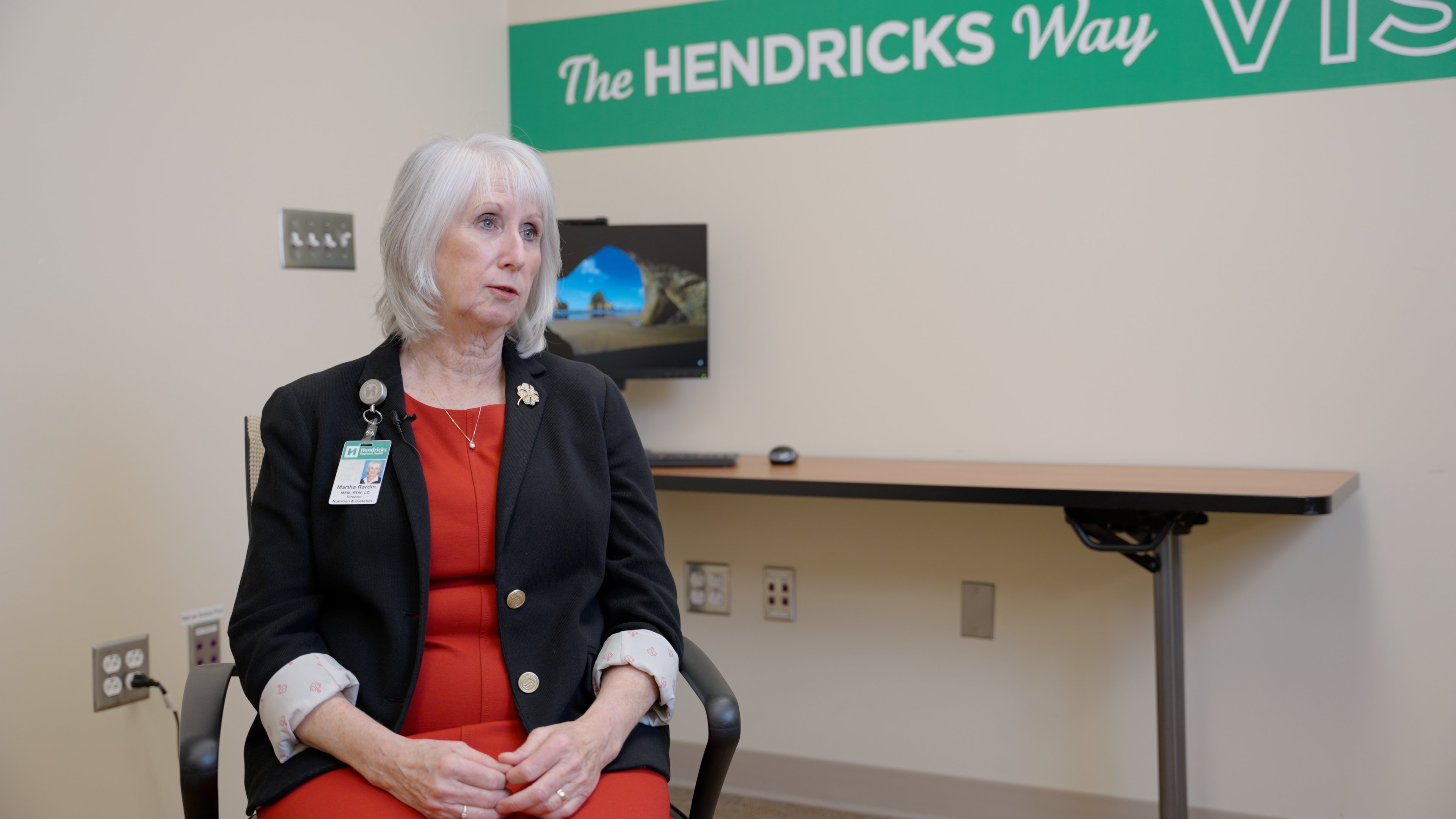
See What Customers Say About Sonicu
Asset Protection. Compliance Automation. And Reduced Manual Processes.
Sonicu serves thousands of professionals at hundreds of organizations across North America by improving how they monitor and manage their most sensitive assets and environments.
Professionals from healthcare, life science, laboratory and cold chain facility management turn to Sonicu to help them improve the way they do business.
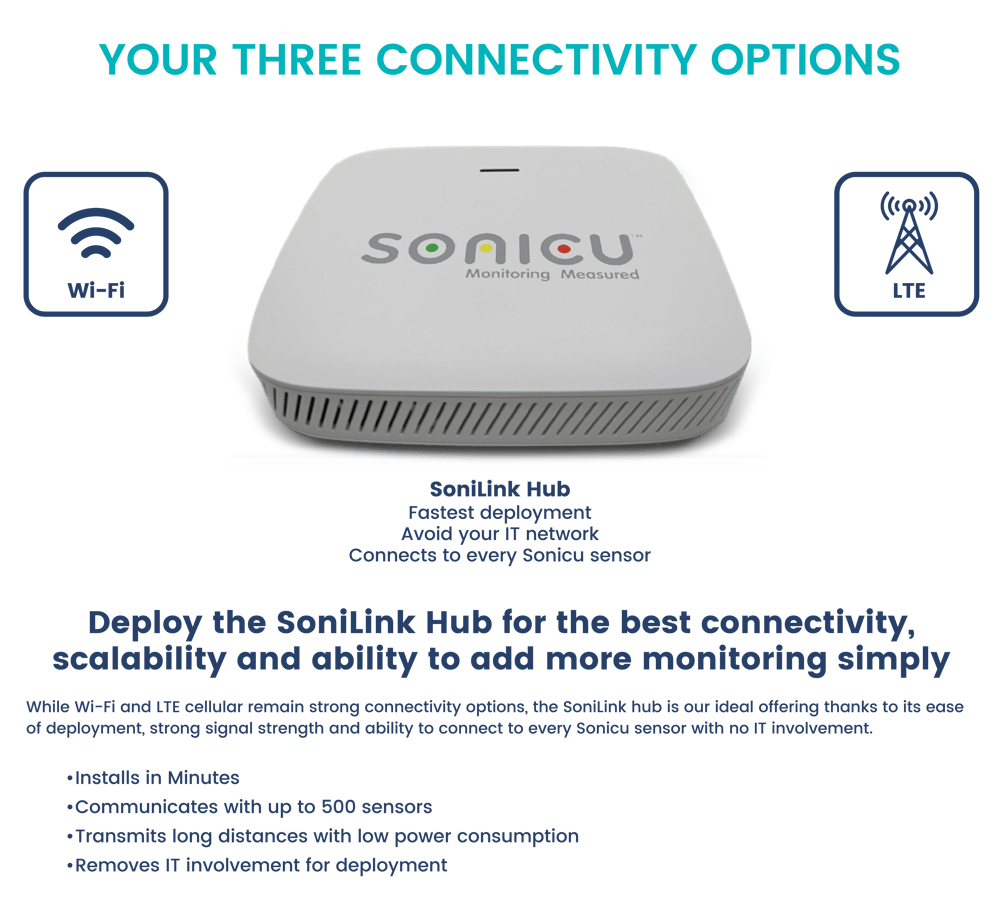
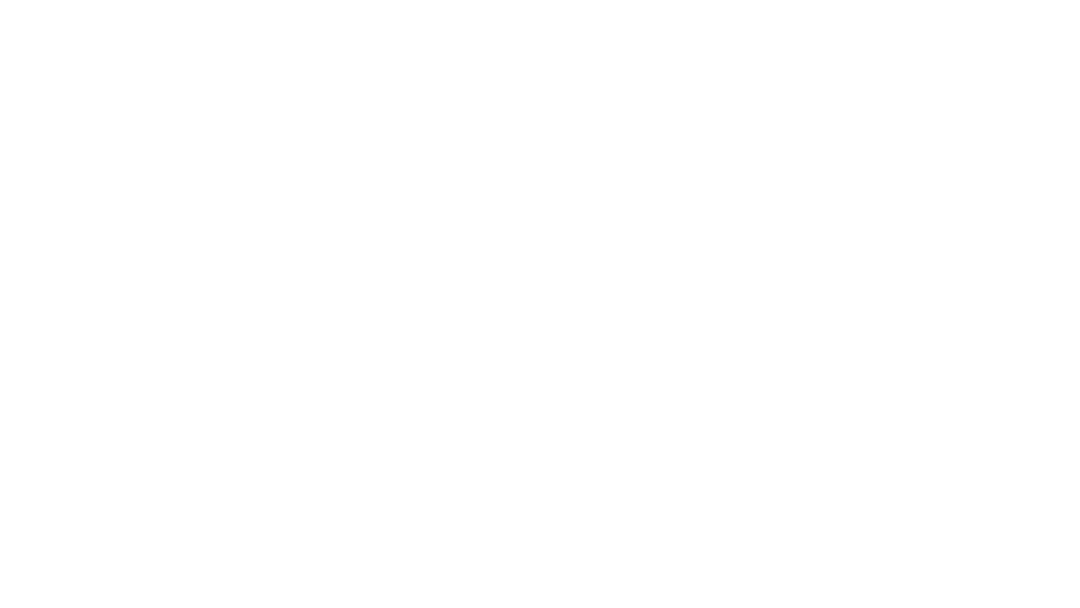
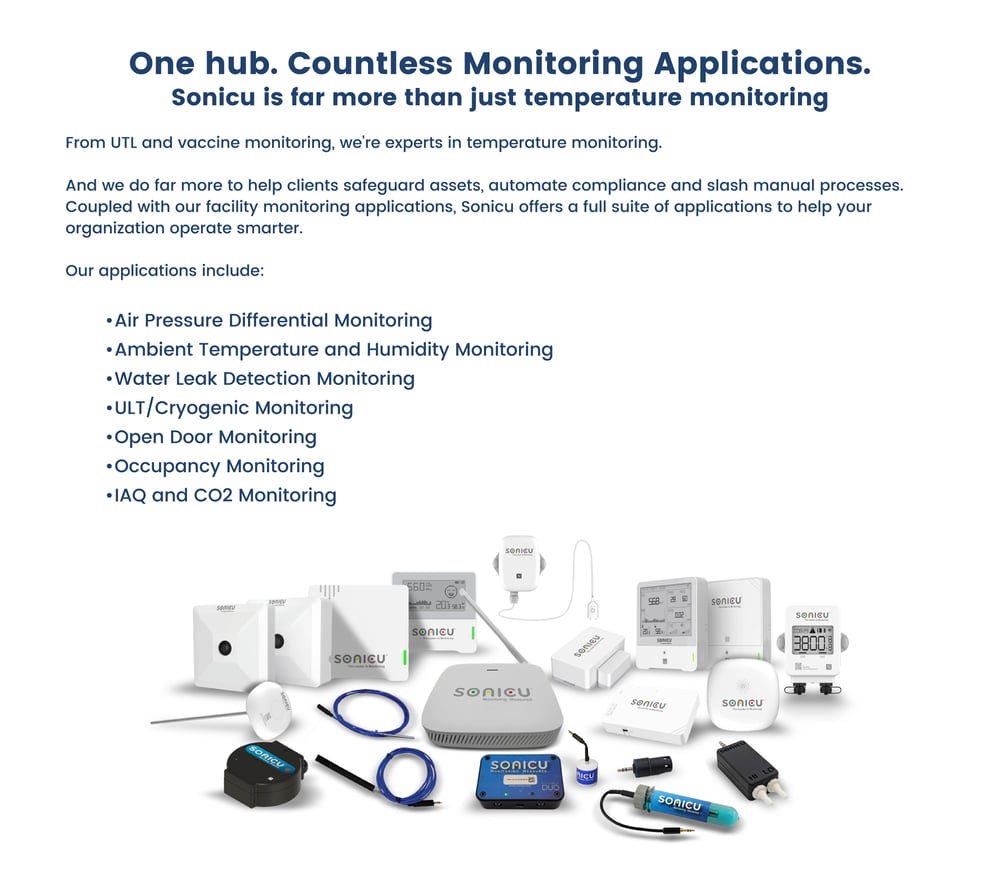
Environmental Monitoring
Environmental conditions are essential to the safety of businesses across numerous industries.
For instance, in industrial manufacturing environments like those within the pharmaceutical sector, monitoring cleanroom environmental conditions is essential to prevent the contamination of valuable materials.
While you may know about the importance of maintaining a consistent environment, seeking cleanroom environmental monitoring solutions is essential to ensure proper compliance that maintains hygiene levels within your workplace.
Many businesses in the healthcare and pharmaceutical industries practice environmental monitoring by the settle plate method. This method refers to the use of settle plates exposed to the air to allow for the collection of particles to assess microorganism levels within an organization’s cleanroom accurately.
The settle plate method principle states that most microorganisms link to individual particles. In the settle plate method, microbiology is vital to understanding the ideal time for exposure to reveal the safety of air conditions in a pharmaceutical setting.
By implementing this method, pharmacies can guarantee that their sensitive work is occurring in viable and safe conditions. Ultimately, ISO guidelines for the settle plate method involve solutions to assess microorganism levels within pharmaceutical organizations to maintain a clean and healthy environment.
Given the importance of safe cleanroom conditions for businesses in the pharmaceutical sector, your pharmaceutical organization must implement quality solutions to protect the safety of everyone impacted by your work.
While the settle plate method is a popular way of testing the environment, pharmaceutical organizations must consider monitoring solutions for cleanrooms to comply with set standards and prevent any impurities that could contaminate products.
Because constant monitoring is vital to address any possible issues in your work environment, solutions like Sonicu are crucial to your organization's overall health and well-being and the people it serves. Sonicu contains various automated monitoring solutions for pharmaceutical businesses to protect valuable assets and guarantee the safety of everyone in the organization.
Cryopoint: Mission-Critical Monitoring
Problem: Cryopoint faced calibration challenges with their legacy monitoring system and issues with a server-based system, putting critical samples at risk.
Solution: Transitioned to Sonicu's SoniCloud and its mobile-first solution, enhancing reliability in monitoring and easing operations.
Ohio University Innovation Center
Problem: Tech and tech-enabled startups at the Innovation Center needed reliable support systems for temperature and environmental monitoring due to the requirements of grant-funded projects.
Solution: Implement Sonicu for comprehensive monitoring of temperature, ambient humidity, and air pressure differential, ensuring necessary protection and compliance.
Hancock Regional Health: Enterprise Monitoring from Sound to Environmental
Problem: Disparate monitoring systems were taxing the staff with many manual processes, leading to inefficiencies and reduced asset protection.
Solution: CEO Steve Long initiated the adoption of a consolidated monitoring program for temperature, environmental, and sound, which automated compliance and reduced manual logging.
Environmental Monitoring ISO 14644
Pharmaceutical cleanrooms must adhere to specific standards to ensure safe and effective practices. The International Standards for Organization (ISO) outline numerous practices for cleanrooms. For example, ISO 14644-1:1999 outlines specific guidelines for maintaining cleanrooms and other controlled environments within the pharmaceutical industry. Specific classifications impact standards for your cleanroom for ISO standards.
For instance, ISO 14644-1 class 8 cleanrooms require different conditions for air changes than class 7 cleanrooms. Depending on what classification your cleanroom falls under, you may adhere to monitoring solutions and practices different from practices standard in other cleanroom classifications.
Monitoring steady conditions in a cleanroom or other controlled environment is further outlined by ISO 14644-2:2015, which states the importance of monitoring solutions to offer evidence of how well a cleanroom performs regarding air cleanliness. Ultimately, ISO standards are crucial to successful environmental monitoring. ISO 14644 prioritizes air cleanliness by viewing cleanliness in terms of how many particles exist within a concentrated volume of air.
Furthermore, ISO 14644 standards are vital to environmental monitoring practices to determine the overall cleanliness of a pharmaceutical organization and ensure the health of everyone within an institution. Adhering to ISO 14644 is simpler when organizations utilize monitoring solutions like Sonicu to ensure constant access to their institution’s environmental condition.
Microbiological Environmental Monitoring Guidelines
Though monitoring solutions are crucial for pharmaceutical institutions, various industries benefit from following microbiological environmental monitoring guidelines appropriate for the products and services individual organizations provide.
For example, organizations operating in the healthcare, life sciences, or food industries require unique monitoring solutions to test the microbiological environment of their institution.
Given the unique requirements of monitoring solutions across different industries, many people face confusion when navigating a generic environmental monitoring guideline.
Finding guidelines tailored to your industry and your organization’s specific monitoring requirements is essential.
If you are seeking solutions like environmental monitoring in the pharmaceutical industry PPT, then you must find guidelines tailored explicitly to pharmaceutical needs. Maintaining consistent environmental conditions is vital to your institution's overall safety and well-being and resources like prescription medications.
However, if you need microbiological environmental monitoring guidelines for the food industry, then resources regarding pharmaceutical companies are of little help. Many monitoring solutions target a specific industry, making it challenging for businesses outside that industry to benefit from monitoring devices.
Providers like Sonicu are adaptable and essential for solving issues in monitoring environmental conditions for healthcare, pharmaceutical, food, and life science businesses. Sonicu is an ideal fit for all your automated monitoring needs because of its broad scope of purposes.
Environmental Monitoring Program
Deciding on the best monitoring solutions for your organization requires thorough knowledge of the purpose of environmental monitoring programs across various industries. An environmental monitoring program is vital to informing businesses like pharmacies of specific policies and procedures crucial to sustaining a safe environment.
Pharmaceutical organizations must be especially cautious when implementing monitoring solutions because of the sensitive nature of materials in a controlled cleanroom environment. Understanding guidelines for an environmental monitoring program is one step toward improved monitoring solutions and safer work practices for all staff members working in a controlled environment.
One program essential for many businesses is the USP 797 environmental monitoring policies. USP 797 is a regulation that governs a vast range of pharmaceutical policies and procedures. When seeking environmental monitoring in the pharmaceutical industry PPT resources, you will likely find information about USP 797.
The regulation helps pharmaceutical businesses reduce infections transmitted to patients through unsafe pharmaceutical products. Furthermore, you will find value in a PDA guidelines download, which describes the critical fundamentals of any successful monitoring solution. USP 797 and PDA guidelines help pharmacies protect working staff members during pharmaceutical exposure.
While USP 797 may not offer as many solutions for those seeking microbiological environmental monitoring guidelines for the food industry, it remains a valuable standard for organizations where cleanroom monitoring is beneficial.
You can learn more about how our software helps compliance professionals in these case studies:
Discount Drug Mart: Power Outage Protection + Compliance Automation
Problem: Transitioning from manual temperature logs and reactive power outage management
Solution: Adopting Sonicu's advanced system for seamless temperature monitoring and real-time power outage alerts across its 77 locations.
Hendricks Health: From Nutrition to the OR
Problem: The need to improve compliance and safety across various departments, starting from nutrition to the operating rooms.
Solution: Upgraded monitoring systems to enhance patient safety and streamline compliance across multiple facilities, including local YMCA rehabilitation facilities.
IU Health: Enterprise Monitoring
Problem: Challenges of using a locally based server and multiple monitoring solutions across departments.
Solution: Transitioned to a single, cloud-based solution with Sonicu to enhance monitoring capabilities across more than a dozen locations and the IU School of Medicine.
Environmental Monitoring In Pharmaceutical Industry
Environmental monitoring in pharmaceutical industry operations is vital for numerous reasons. While monitoring solutions are necessary to ensure safe conditions for pharmaceuticals at risk of damage from outside contamination, these solutions are equally important to the individuals working directly with the materials.
Area monitoring in pharmaceutical industry operations is crucial to ensuring the health and safety of everyone in an organization.
Environmental monitoring solutions may differ slightly based on the unique needs of your pharmaceutical business. For example, environmental monitoring in the pharmaceutical industry USP guidelines prioritizes reducing infections transmitted to patients through unsafe practices.
Environmental monitoring in the non-sterile pharmaceutical industry will require different solutions than those for sterile storage areas regarding conditions like differential pressure.
A generic search for “environmental monitoring in pharmaceutical industry PPT guidelines” will fail to yield high-quality results relevant to your organization. Given the sensitive nature of materials handled by pharmacies, your institution needs advanced solutions for microbial environmental monitoring.
In pharmaceutical industry operations, intelligent monitoring solutions are everything. Whether or not your monitoring solutions are thorough and competent is a make-or-break situation for your institution.
Advanced solutions like Sonicu allow for complete control over your monitoring and constant access to essential reports regarding environmental conditions in your workplace.
PDA Guidelines For Environmental Monitoring
The Parenteral Drug Association (PDA) is essential to understanding the importance of practical technical information to ensure safe pharmaceutical practices and regulations. PDA guidelines for environmental monitoring are crucial to following current industry standards and protecting the health of staff and consumers.
Though environmental monitoring USP guidelines are also essential to your monitoring solutions, the PDA is tailored to pharmaceutical organizations and works to advance manufacturing science and regulation in the pharmaceutical industry.
PDA guidelines are vital to guarantee that your organization is up to date on the latest regulations to foster a safe and healthy work environment.
PDA solutions are scientifically sound and consist of practical technical information and expertise that benefits pharmaceutical businesses and safeguards the health of everyone involved in the pharmaceutical manufacturing process.
Environmental monitoring pharma guidelines are valuable to any organization managing pharmaceutical substances that bacteria could significantly damage without safe environmental conditions.
Any successful pharmaceutical or biopharmaceutical organization will understand the importance of practical technical information to advance manufacturing science and regulation.
PDA fundamentals of an environmental monitoring program outline resources and practices crucial to monitoring controlled environments when manufacturing pharmaceutical products and cleanroom resources.
Furthermore, monitoring solutions like Sonicu are vital because they adhere to the PDA's best practices for monitoring environmental conditions in pharmaceutical organizations.
FDA Guidance Environmental Monitoring
Following proper guidelines for monitoring environmental conditions in your pharmaceutical organization is vital. However, FDA sampling guidelines are among the essential solutions to adhere to if you are operating in the pharmaceutical industry.
Environmental sampling microbiology is crucial to analyzing an organization’s environmental conditions and determining whether an institution has safe practices.
Pharmaceutical organizations collect numerous environmental samples for further analysis during environmental sampling.
When completed following FDA guidance, environmental monitoring and sampling can guarantee the safety of an organization and anyone involved in the manufacturing process.
FDA guidelines also cover specific FDA guidance on environmental monitoring of non-sterile areas. Given the potential danger of managing non-sterilized materials, it is crucial to know how to operate and manipulate non-sterile materials during sampling.
When you fail to adhere to FDA guidelines and regulations, you put yourself and your organization at risk of faulty monitoring, poor conditions, and health risks.
Though following FDA guidelines may seem simple, it is essential to implement monitoring solutions that adhere to the standards set by the FDA.
Sonicu is valuable because its advanced monitoring solutions eliminate manual errors while providing around-the-clock access to monitoring, alerting, logging, and reporting capabilities.
By implementing Sonicu, pharmaceutical organizations can conduct safe, protected, and risk-free business practices.
American-based Customer Support: Robust & Reliable High Touch Service
Software and technology is only as good as the people who stand behind it.
At Sonicu, that means our team of American-based customer success managers who are never more than a phone call away to help field and fix any service issues.
Our probes and sensors are placed in demanding frozen environments and our software literally sends billions bits of data monthly, meaning there’s alway the potential for a hiccup on either the hardware or software.
We are committed to fielding every customer service request promptly and addressing our customer’s concerns promptly and professionally.
“I like to say that every refrigerator or freezer is like a car in that they all behave a bit differently, and then every now and then you just get a bad boy who doesn’t want to perform as we need it to. Sonicu has been a powerful tool to identify which units are behaving out of spec and get our team to fix them before we have a serious issue.”
Martha Rardin, Director, Nutrition and Dietetics, Hendricks Regional Hospital.
“In the current era of supply chain challenges, tossing drugs is more than a financial loss. Healthcare leaders can no longer predictably rely on suppliers to be able to replenish supplies with the same just-in-time predictability that existed prior to COVID-19.”
Tim Livesay, Director, Hancock Regional Hospital Pharmacy Director
We realized there had to be a better way and went in search of technology that could give us that level of monitoring that would keep our patients safe. Sonicu made it easy and we grew across the entire hospital.