Cleanroom Monitoring System
If you are looking for an cleanroom monitoring system that helps you and your team eliminate manual logging, improve compliance readiness, and protect all your temperature-sensitive assets, you’ve arrived at the right place.
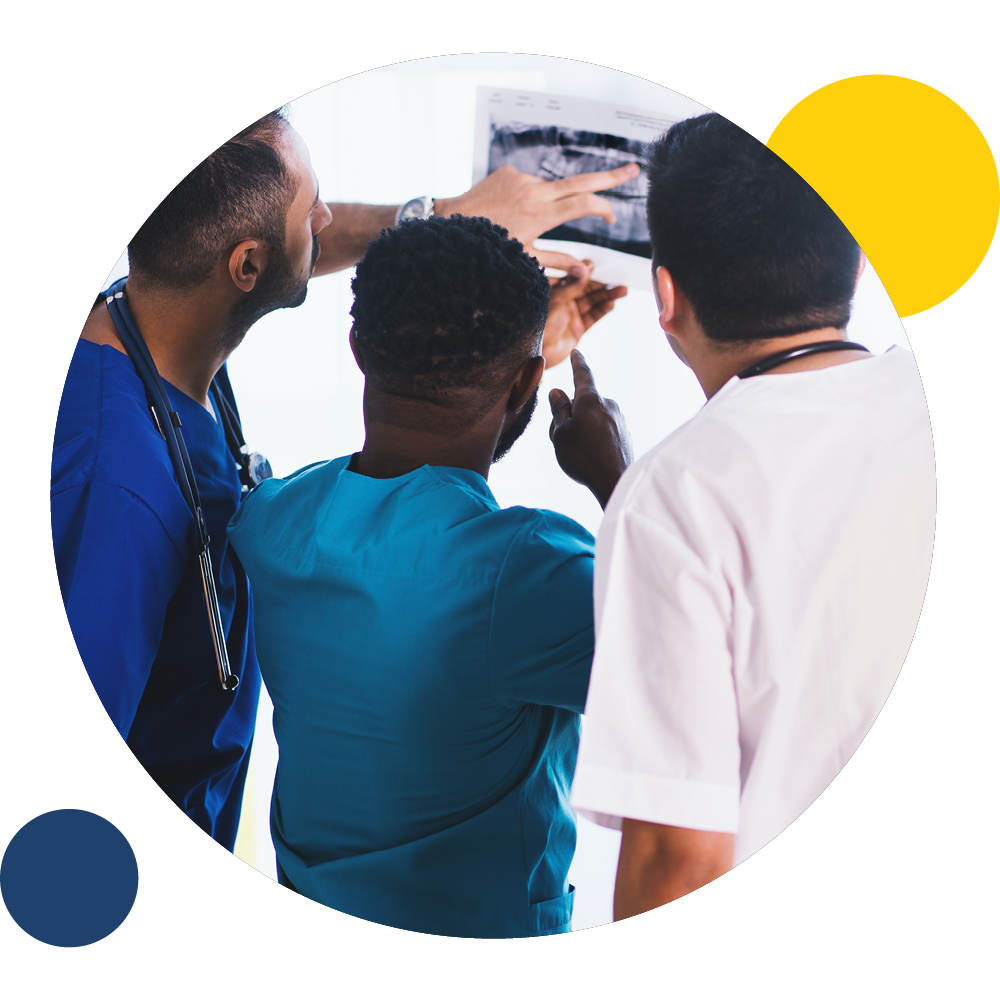
Let us help you evaluate your needs!
- Safety: Alerts to protect assets
- Compliance: Automated reports
- Efficiency: Reduced Manual Logging
And what makes us different?
- Lifetime Warranty: Never buy hardware again!
- Unlimited Users: Scale across your entire org
- Connectivity Flexibility: Wi-Fi, Cellular or Data Hub
- Phone call alarms: Alerts won't get ignored
- Mobile App: 500 Freezers in your pocket
All American made and supported!
See What Customers Say About Sonicu
Asset Protection. Compliance Automation. And Reduced Manual Processes.
Sonicu serves thousands of professionals at hundreds of organizations across North America by improving how they monitor and manage their most sensitive assets and environments.
Professionals from healthcare, life science, laboratory and cold chain facility management turn to Sonicu to help them improve the way they do business.
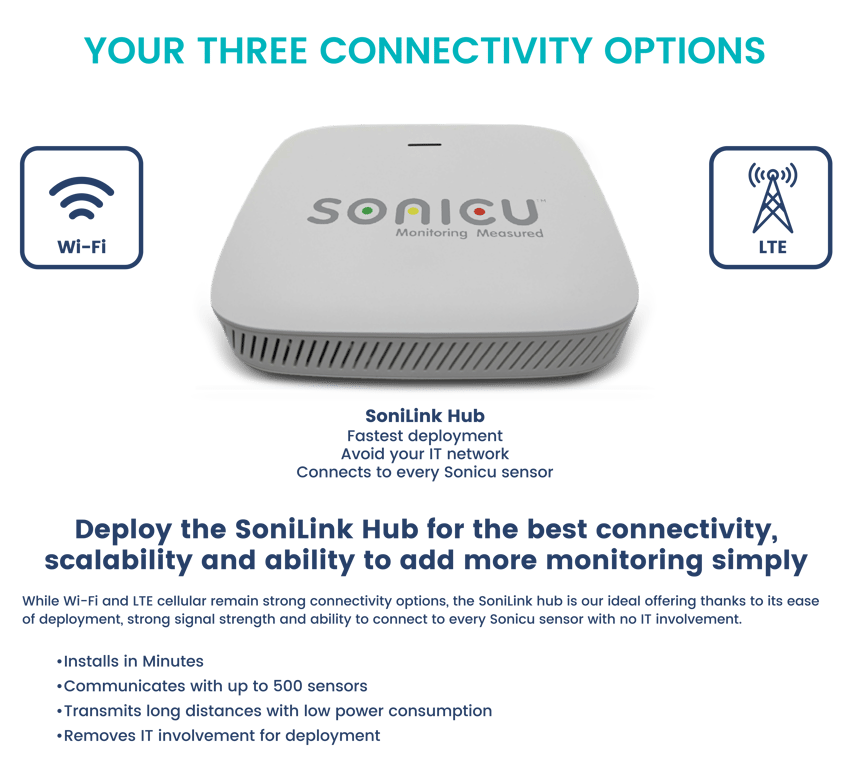
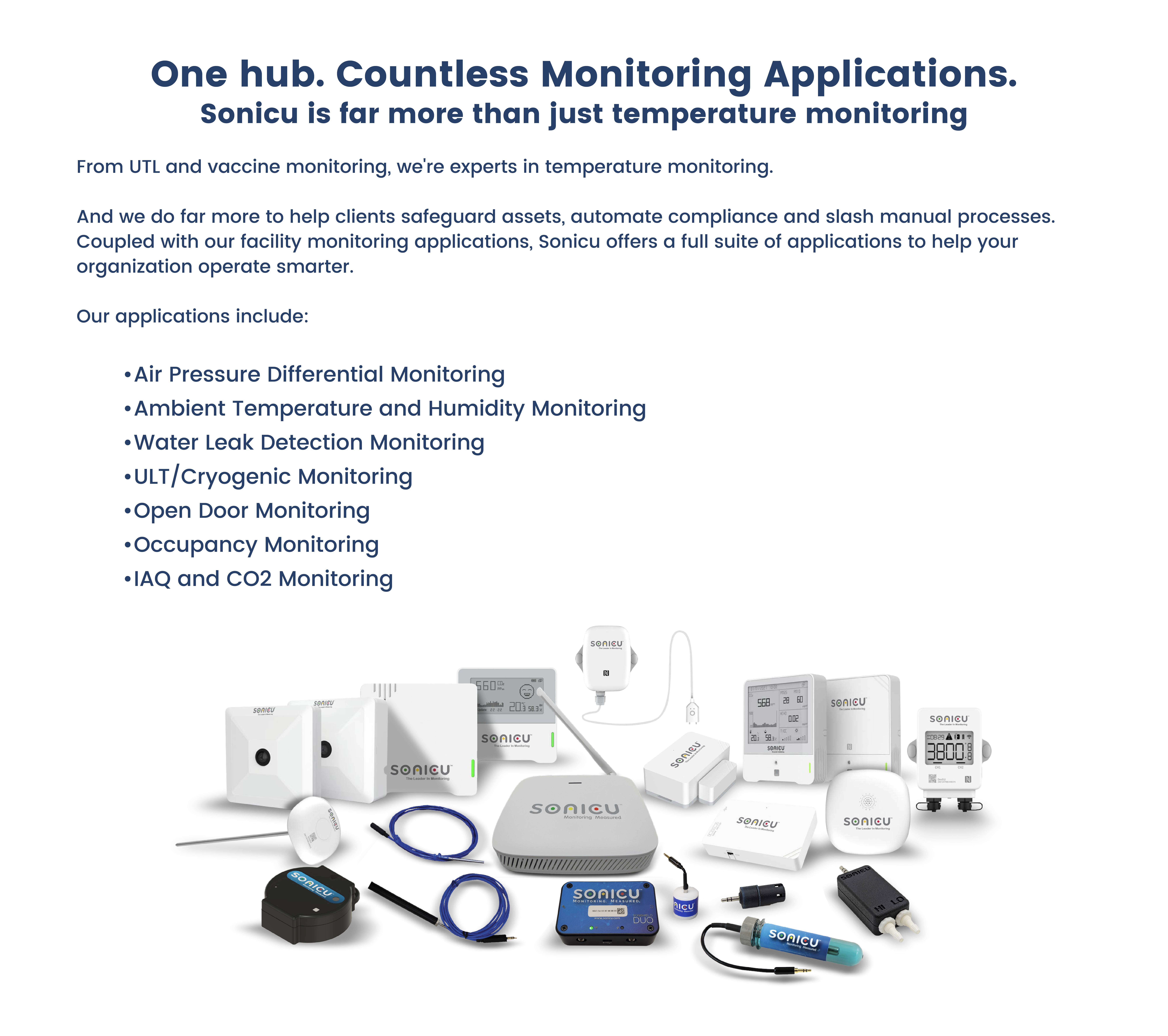
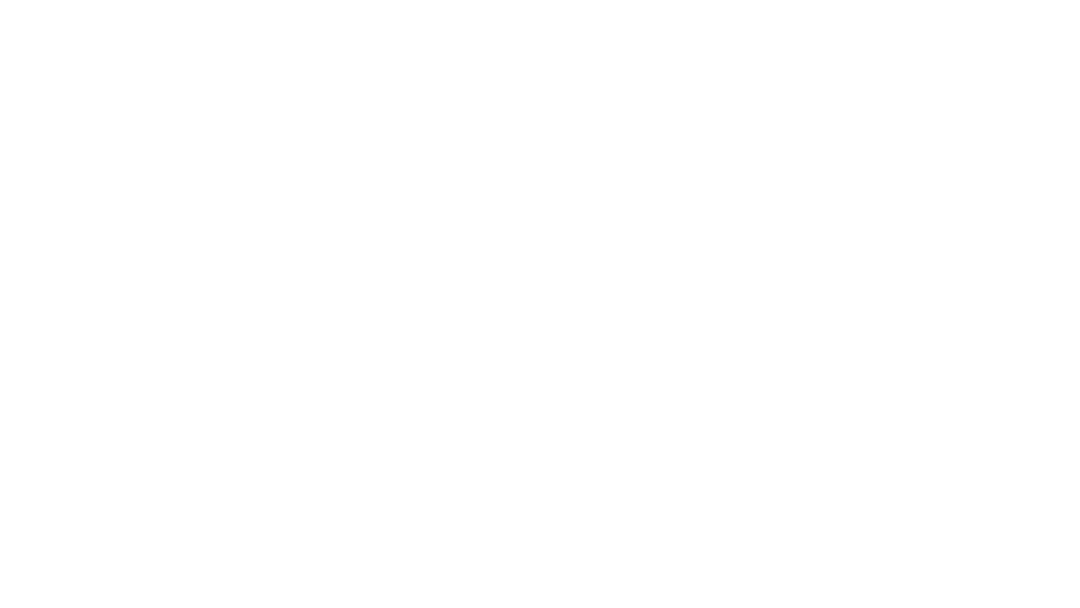
Cleanroom Monitoring System
Some of the finest names in healthcare, including Indiana University Health, University of Michigan Health System, and Stanford University rely on Sonicu to provide a robust and continuous environmental monitoring system, including temperature, humidity, air pressure, and more.
These respected healthcare and research brands turn to Sonicu for four primary reasons:
- Real-Time Monitoring: the sensors collect temperature, humidity, air pressure data, and more, and transmit it wirelessly to SoniCloud - our cloud-based platform.
- Operational Efficiency: Virtually eliminate the need for tedious and costly manual logging
- Compliance Automation: Respond to any regulatory audit or inspection in a few clicks with our reports section
- Asset Protection: Detect and respond to any threshold that can threaten anything perishable: food, drugs, vaccines, research, etc.
Our customers stay with us thanks to our American-based customer support, which is never more than a phone call away. While our technology is intuitive and powerful, we know it’s only as strong as the people who stand behind it.
Cleanroom monitoring systems are instrumental in maintaining a sterile environment in industries requiring precise control over ambient conditions.
These sophisticated systems play a pivotal role, particularly in the pharmaceutical sector, where the highest level of cleanliness is paramount to protecting product integrity, guaranteeing safety, and complying with strict regulatory guidelines.
Cleanroom monitoring systems are designed to provide real-time tracking of airborne particles and environmental conditions, including temperature, humidity, differential pressure, and more.
This continuous scrutiny allows for immediate correction in case of any deviations, ensuring the production process is not compromised and containment does not occur.
The best cleanroom monitoring systems offer advanced features like automated alarm notifications, in-depth data reporting, dynamic trending, and compliance with rigorous international norms like ISO 14644 or EU GMP Annex 1.
These systems not only guard against contamination and help overcome the challenges inherent in creating sterile products but also offer valuable benefits such as greater operational efficiency, reduced waste, and enhanced product quality.
Understanding the clean room monitoring requirements is crucial for industries that rely on these systems. Appropriate monitoring strategies should be implemented based on the specific activities performed within the cleanroom, the risk to the product, and the regulatory requirements for the product.
Implementation of a robust monitoring plan can significantly safeguard product quality, reduce recalls, and instill confidence in regulators, clients, and patients about the validity of the process and product.
Sonicu provides a comprehensive cleanroom monitoring system suitable for various applications.
- With Sonicu, real-time, cloud-based data monitoring meets or exceeds all compliance and regulatory requirements.
- Their system not only flags issues instantaneously but also provides predictive measures to prevent potential problems.
- The versatility and effectiveness of Sonicu's monitoring systems make them a pivotal tool for industries, especially the pharmaceutical sector, to maintain their cleanrooms and produce high-quality products.
A cleanroom monitoring system is an essential tool for industries to maintain stringent cleanliness standards. The pharmaceutical sector, in particular, stands to benefit enormously from these advanced systems.
Sonicu products, with their robust features, offer a formidable solution to the challenge of maintaining absolute control over environmental conditions in a cleanroom.
Cost Factors Of Cleanroom Monitoring Systems
Cleanroom monitoring systems are a crucial aspect of maintaining highly scrutinized cleanliness standards within industries such as pharmaceutical and semiconductor production. These systems go above and beyond conventional monitoring techniques, helping to ascertain optimal compliance with regulatory standards.
While the benefits of cleanroom monitoring systems are undoubtedly significant, it's essential to consider distinct cost factors tied to their adoption and utilization, which can vary from one setting to another.
The cost factors of cleanroom monitoring systems encompass several peculiarities. These include initial capital expenditure, the cost of maintenance and calibration, cost variations based on the room's size, and the overall operational cost.
An often-used tool in determining these costs upfront is the use of a cleanroom monitoring system cost calculator. This device allows potential users to anticipate and budget for the system's incorporation within their operational processes.
Additionally, users may also ponder the cost metrics in relation to the room's square footage. By considering the cost per square foot of the cleanroom monitoring system, the management can better understand the coverage and value derived from the system.
It is also crucial to remember that these costs could fluctuate depending on whether the cleanroom monitoring systems are being set up in new facilities or retrofitted in an existing one.
Sonicu, as an industry-leading solution provider, efficiently caters to these varied cost considerations. Their cloud-based system requires minimal investment and upkeep, making it a cost-effective choice for organizations of all sizes.
Cleanroom monitoring systems' costs may also be influenced by the type of industry, the level of accuracy required, and the level of automation. Highly automated systems tend to be pricier but may prove economical over the long term due to reduced labor costs and enhanced efficiency.
Sonicu’s automated, real-time monitoring, coupled with instant notifications and customizable alarms, ensures efficiency while contributing to the cost-savings aspect of an organization's operations.
Understanding the cost factors of cleanroom monitoring systems helps organizations make informed decisions, maintain regulatory compliance, and maximize operational efficiency without compromising on budgetary parameters.
Every organization must evaluate these factors meticulously before considering the incorporation of such sophisticated systems into their workflow.
With Sonicu, organizations can anticipate comprehensive solutions attuned to their specific needs, thereby making the most of their investment in cleanroom monitoring systems.
Companies such as Nomi Health have trusted Sonicu to provide them with peace of mind when it comes to temperature monitoring. Other benefits they receive by choosing Sonicu include:
- Asset Protection: Get alerts when a freezer is malfunctioning to protect assets like medicines, vaccines, blood, research, sperm/eggs
- Compliance Automation: Creates simple reports to satisfy local/state/federal regulations
- Operational Efficiency: Spend less time capturing data manually: Both temps/conditions and reporting
Cleanroom Systems In the Pharmaceutical Industry
Understanding the significance and utilization of cleanroom systems in the pharmaceutical industry is imperative.
These systems are specifically designed to maintain an aseptic environment that enables researchers and manufacturers to perform critical tasks without the threat of contamination.
They adhere to stringent pharmaceutical clean room classification standards to ensure optimal quality control and compliance with regulatory agencies.
Sonicu, being a leading provider of environmental monitoring solutions, enables industries, including pharmaceuticals, to maintain the highest standards with their state-of-the-art cleanroom systems.
Robust environmental monitoring within the pharmaceutical industry is essential to validate that the necessary conditions in cleanrooms remain within acceptable limits.
Environmental monitoring in pharmaceutical industry guidelines establishes standardized methods to ensure cleanliness, microbial levels, temperature, humidity, and particle counts are accurately monitored.
A proper monitoring system facilitates real-time data collection, immediate alerts for unusual conditions, and extensive reporting options.
With Sonicu's advanced sensors and cloud-based platform, industries get real-time, 24/7 access to comprehensive environmental data, optimizing pharmaceutical operations and safeguarding regulatory compliance.
Diving further into the intricacies of environmental monitoring, numerous system types exist. Types of environmental monitoring in the pharmaceutical industry range from particulate and microbial monitoring to temperature and humidity controls.
Each plays a crucial role in maintaining an ideal production environment, ensuring the safety and efficacy of pharmaceutical products.
Sonicu's range of wireless sensors covers a comprehensive list of environmental parameters, offering complete environmental control and ensuring products and processes align with the highest quality standards.
To provide an environmental monitoring system in the pharmaceutical industry, for example, a cloud-based, wirelessly integrated system might continuously document and alert about changes while providing an organized database of all collected information.
This enhances recall measures, ensures error-free data management, optimizes process efficiency, and aids in maintaining complete control over manufacturing spaces.
Sonicu uniquely combines optimum sensor technology with a cloud-based platform, ensuring seamless data access and alerting system, thereby guaranteeing industry-wide best practices for pharmaceutical production environments.
Hamilton County, Indiana Health Department has entrusted Sonicu and received these top features:
- American-based Customer Service and Tech Support
- Redundancy of Power/Connectivity to protect data integrity
- SNAP calibration service for NIST compliance
- Hardware assembled in the United States
- Built on AWS Cloud for simplicity, speed, reliability, and scalability
Cleanroom Systems In the Healthcare Industry
Cleanroom systems play an exceedingly pivotal role in the healthcare industry, where hygiene standards are exceptionally high.
These meticulously designed areas serve to minimize the presence of environmental pollutants like dust, airborne microbes, and aerosol particles, thereby reducing the risk of contamination.
Integrated with state-of-the-art technology, these cleanroom systems serve preventative, detective, and corrective functions with acute precision, thereby assuring optimum performance across the board.
In the field of pharmaceutical manufacturing, it's imperative to have a robust environmental monitoring system in place.
Navigating under the interdisciplinary umbrella of microbiology and environmental science, environmental monitoring guidelines in the pharmaceutical industry are set with acute precision to ensure uninterrupted production quality and efficacy.
Adhering to these meticulous standards helps in the early detection and mitigation of potential microbiological and particulate contamination, making it a central tenet of product integrity and patient safety.
Sonicu, with its all-encompassing monitoring technology, integrates seamlessly within this intricate framework, providing real-time data monitoring coupled with automated alerting and reporting. This consistency in monitoring promotes a high level of assurance in quality and compliance.
Sonicu's wireless technology supports pharmaceutical clean room classifications by providing reliable data promptly.
Environmental monitoring in the pharmaceutical industry (USP) is a key guideline that sets the standards for quality and purity in drugs, food ingredients, and dietary supplements.
These USP standards provide an efficient regulatory framework that assures cleanroom systems are maintained efficiently, thereby ensuring that all pharmaceutical products are of the highest quality.
Sonicu's platform provides environmental monitoring solutions that align with USP standards seamlessly, ensuring consistent quality management.
Various types of environmental monitoring systems are used in the pharmaceutical industry, each vested according to needs and cleanroom classifications.
Viable and non-viable particle monitoring, temperature and humidity monitoring, differential pressure monitoring, and air velocity or air change rate monitoring are some of the key facets that are measured and controlled in real time.
Sonicu's systems offer all these monitoring types, ensuring an all-encompassing solution for cleanroom systems in healthcare industry requirements.
Sonicu's comprehensive solutions help operationalize the essence of these keywords, delivering top-tier solutions that revolve around efficiency, control, and regulatory compliance, ultimately reinforcing pharmaceutical and healthcare industry standards.
IU Health: Enterprise Monitoring
Problem: Challenges of using a locally based server and multiple monitoring solutions across departments.
Solution: Transitioned to a single, cloud-based solution with Sonicu to enhance monitoring capabilities across more than a dozen locations and the IU School of Medicine.
Great Lakes Bay Health Centers: Immunization Monitoring
Problem: Need for a reliable temperature monitoring solution for vaccines across multiple locations and cold storage devices.
Solution: Implemented Sonicu's automated monitoring and done-for-you calibration, which allows routine checks from mobile devices and ensures compliance with minimal staff involvement.
SUNY Downstate: Protecting Children's Vaccines
Problem: The need for a simple, reliable, and cost-effective monitoring solution after an incident involving an open fridge door nearly costing a clinic a batch of vaccines.
Solution: Adopt a new monitoring system that is easy to install and use, ensuring the safety of vaccine supplies.
American-based Customer Support: Robust & Reliable High Touch Service
Software and technology is only as good as the people who stand behind it.
At Sonicu, that means our team of American-based customer success managers who are never more than a phone call away to help field and fix any service issues.
Our probes and sensors are placed in demanding frozen environments and our software literally sends billions bits of data monthly, meaning there’s always the potential for a hiccup on either the hardware or software.
We are committed to fielding every customer service request promptly and addressing our customer’s concerns promptly and professionally.
“I like to say that every refrigerator or freezer is like a car in that they all behave a bit differently,
and then every now and then you just get a bad boy who doesn’t want to perform as we need it to,”
Martha Rardin, Director, Nutrition and Dietetics, Hendricks Regional Hospital.
“Sonicu has been a powerful tool to identify which units are behaving out of spec and get our team
to fix them before we have a serious issue.”
Tim Livesay, Director, Hancock Regional Hospital Pharmacy Director
How IU Health
consolidated all of its pharmacy monitoring needs
into one cloud-based platform serving dozen of locations.